Acción Performance is a strategic partner in supply chain production solutions that utilizes the power of scalable, diverse workforces to maximize efficiency. We tackle your non-core business to optimize your current process and drive success to your bottom line.
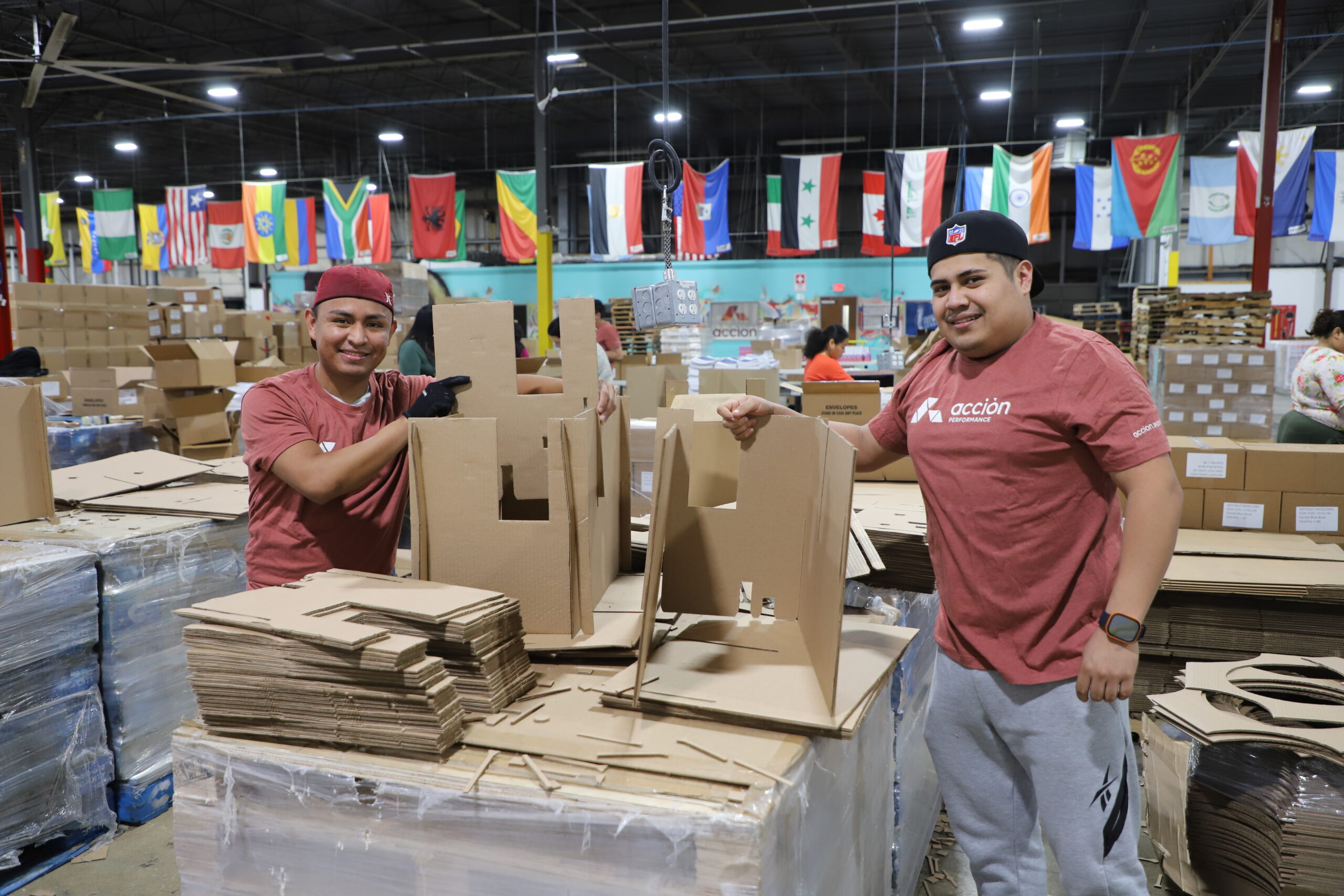
Our Supply Chain Solutions
Partnering with Acción Performance allows your business to remain agile as production needs shift. Our customized solutions eliminate wasted resources by optimizing performance as we seamlessly integrate into your logistics processes.
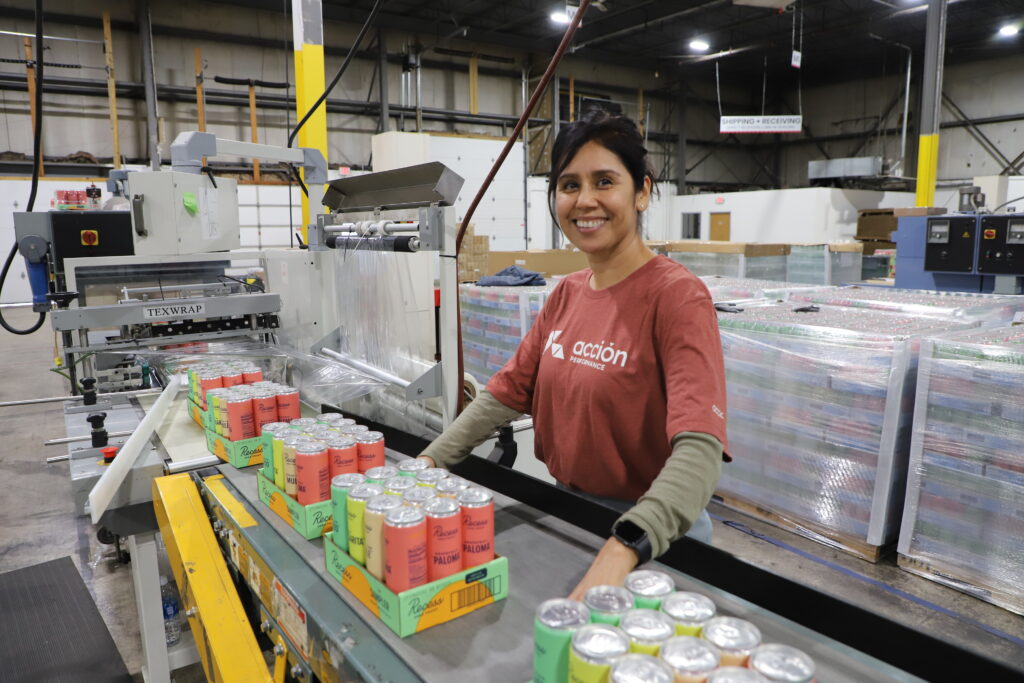
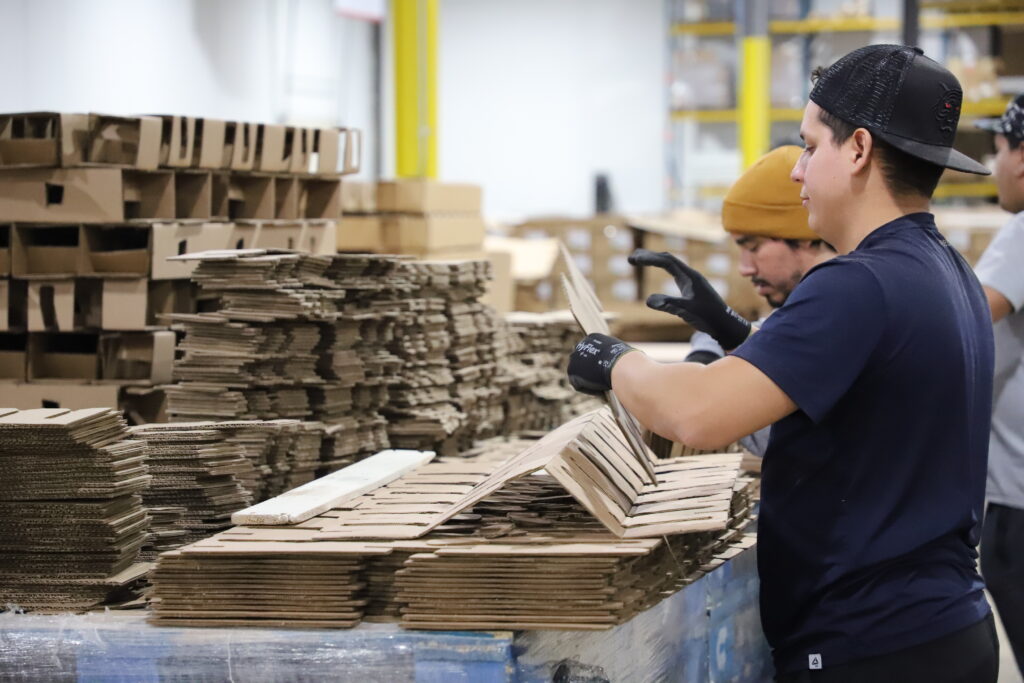
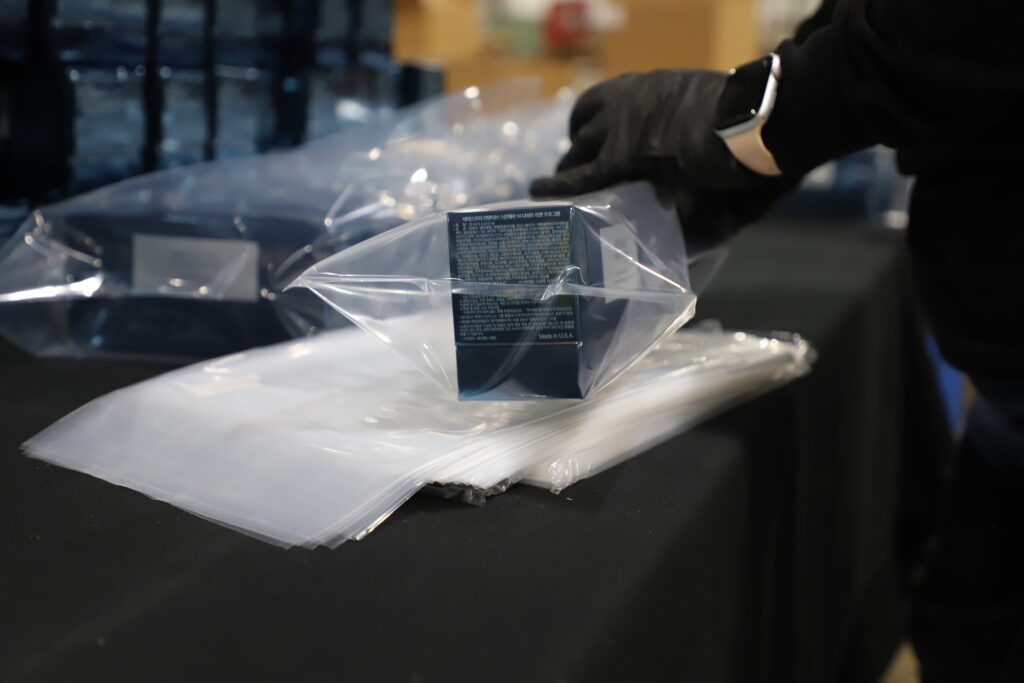
Packaging Solutions
Stay on top of product alterations and capitalize on packaging as a marketing tool to your clients. Our team can focus on product appearance while ensuring safe and secure delivery to its destination.
OUR CAPABILITIES
- 3PL Fulfillment
- FBA Prep
- Kitting and Assembly
- Repack and Rework
- Display Builds
- Co-packing
- Labeling and Stickering
- Sortation
- Shrink Wrapping
- Primary and Secondary Packaging
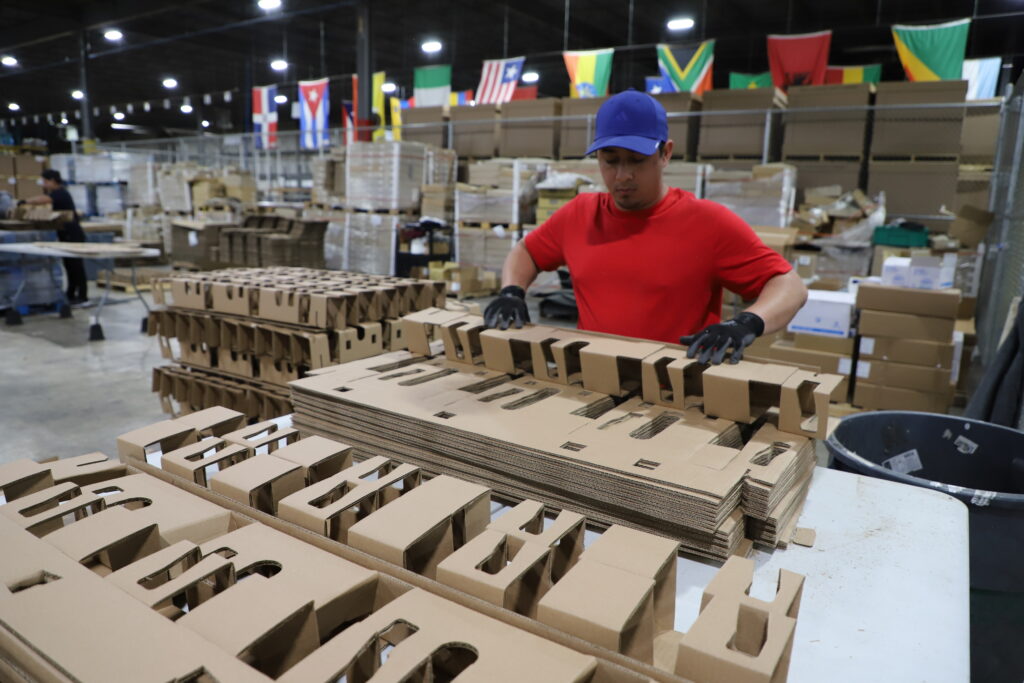
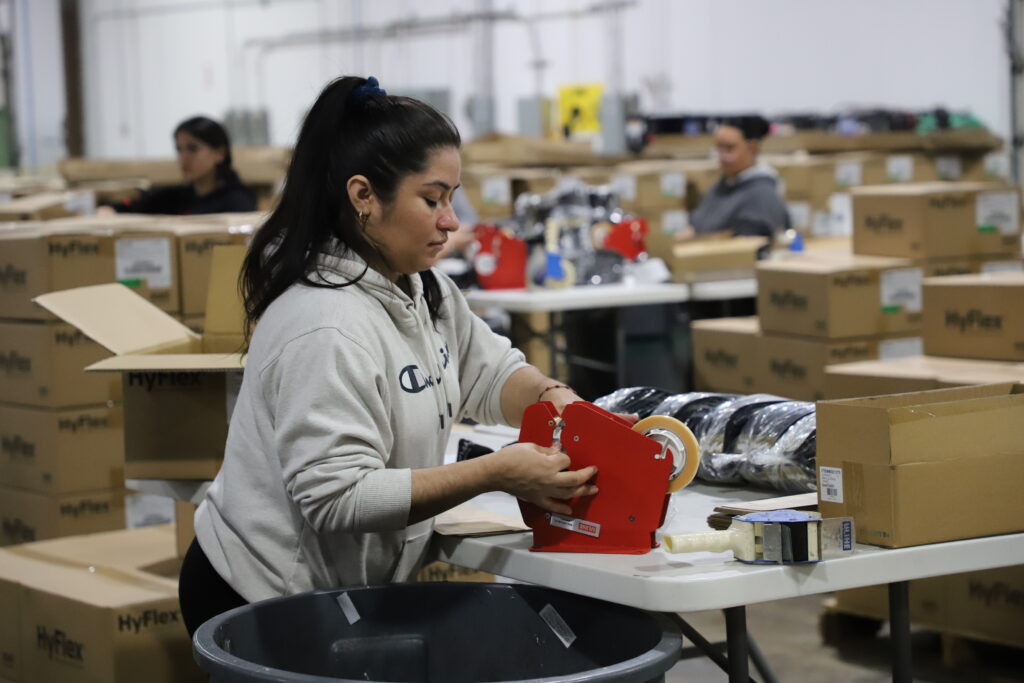
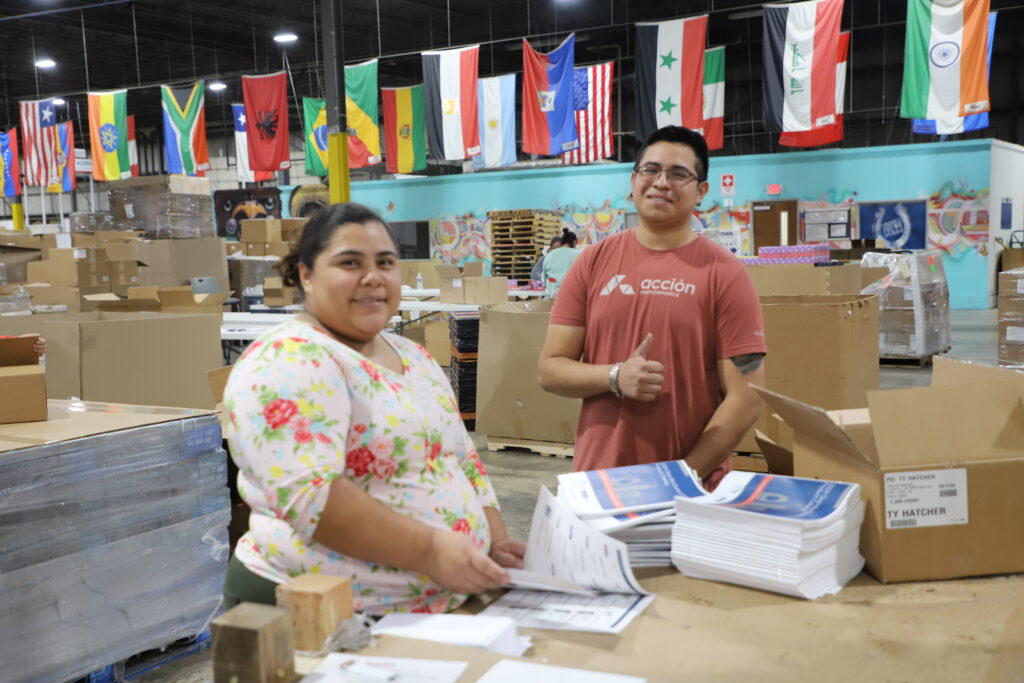
Assembly & Co-Manufacturing Solutions
Reduce overhead costs and boost speed to market by shifting your assembly and co-manufacturing tasks to the Acción team. Our skilled team prioritizes quality and safety at every step.
OUR CAPABILITIES
- Kitting & Assembly
- Labeling & Stickering
- Quality Inspection
- Sortation
- Repack & Rework
- Display Builds
- Shrink Wrap & Secondary Packaging
- Incentives & Loyalty Marketing
- Returns Refurbishing
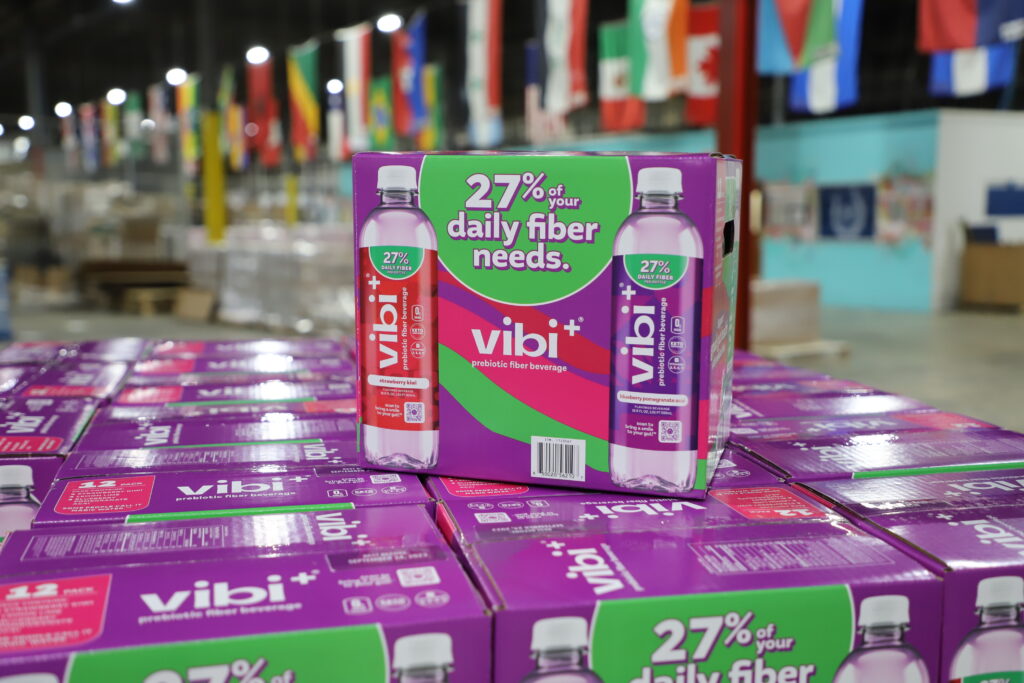
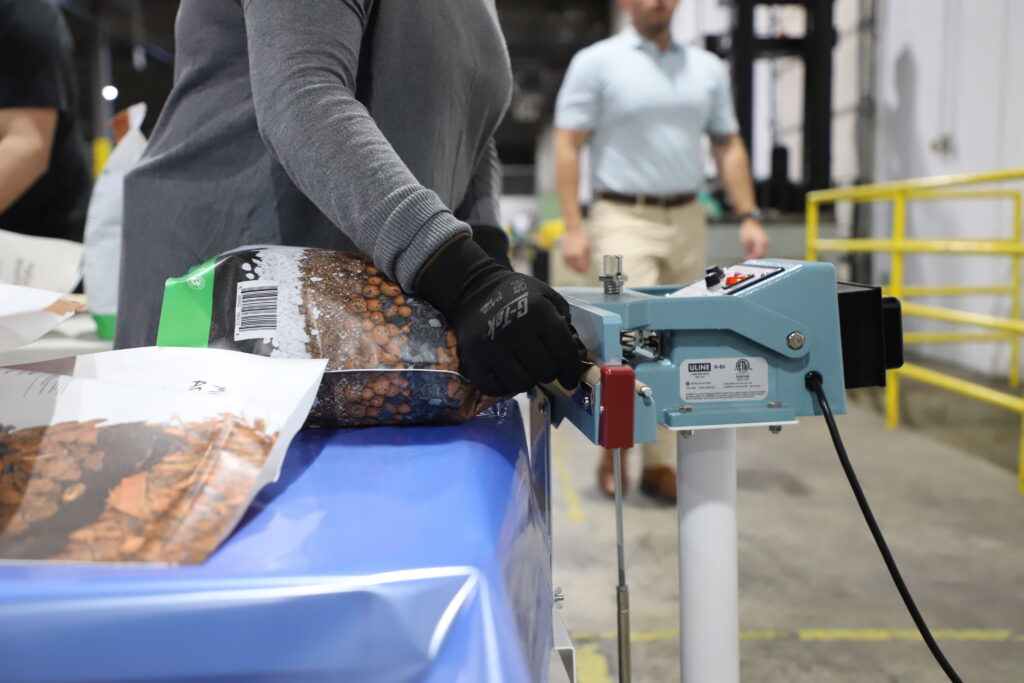
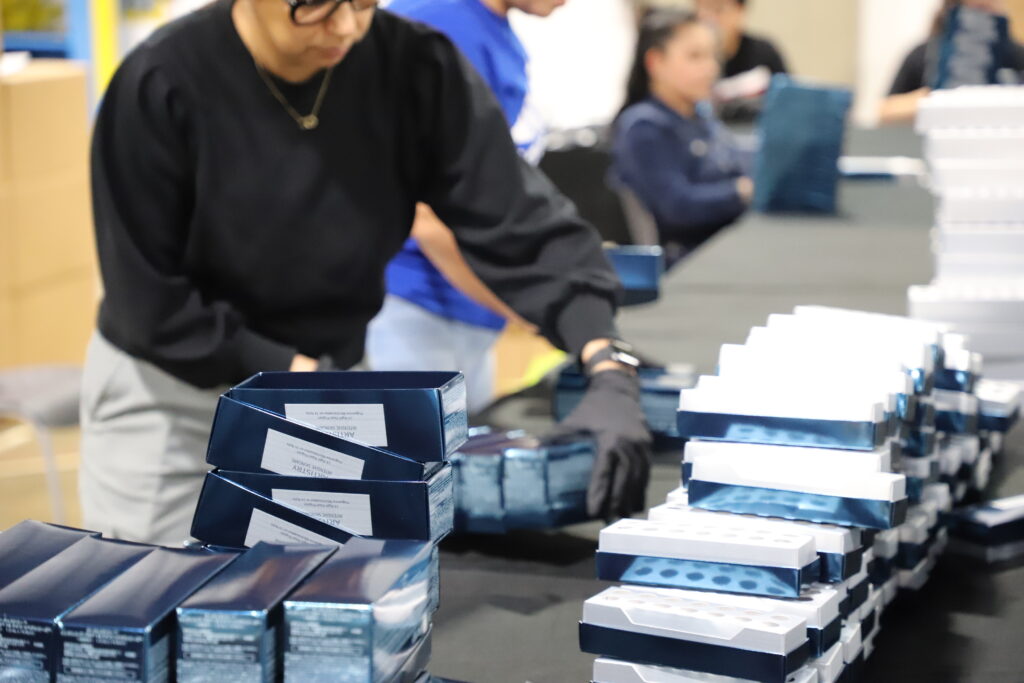
Fulfillment by Amazon (FBA) Prep
Ensure your products are properly packaged and sent on time for Fulfillment by Amazon. Acción Performance prepares your items to fit necessary requirements, saving your team extra time and valuable resources.
OUR CAPABILITIES
- Kitting & Assembly
- Labeling & Stickering
- Quality Inspection
- Sortation
- Shrink Wrap & Secondary Packaging
- Repack & Rework
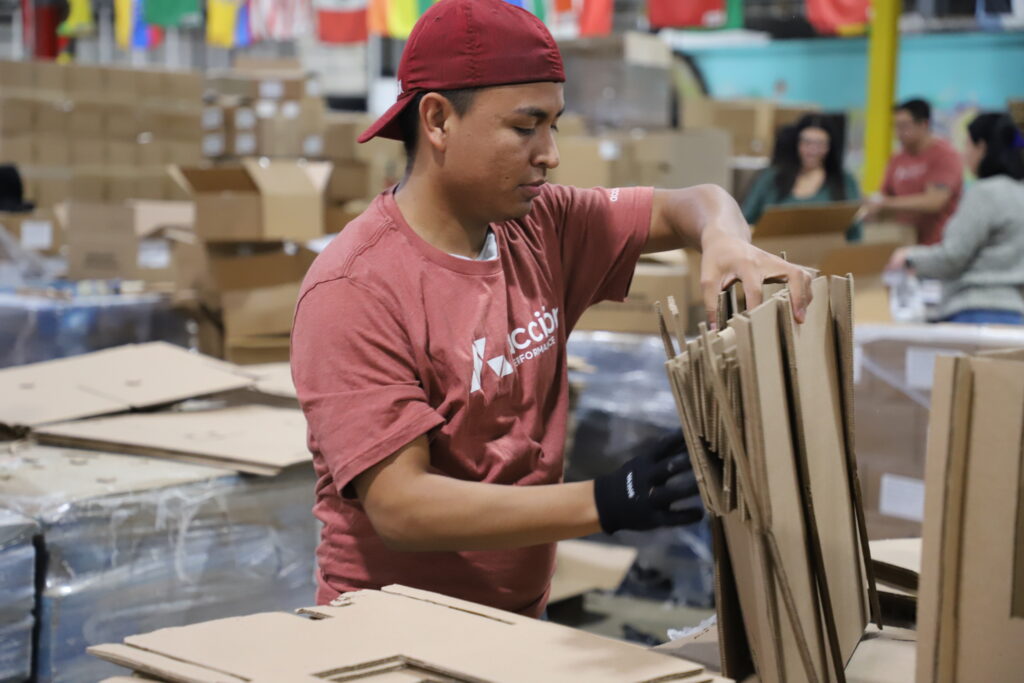
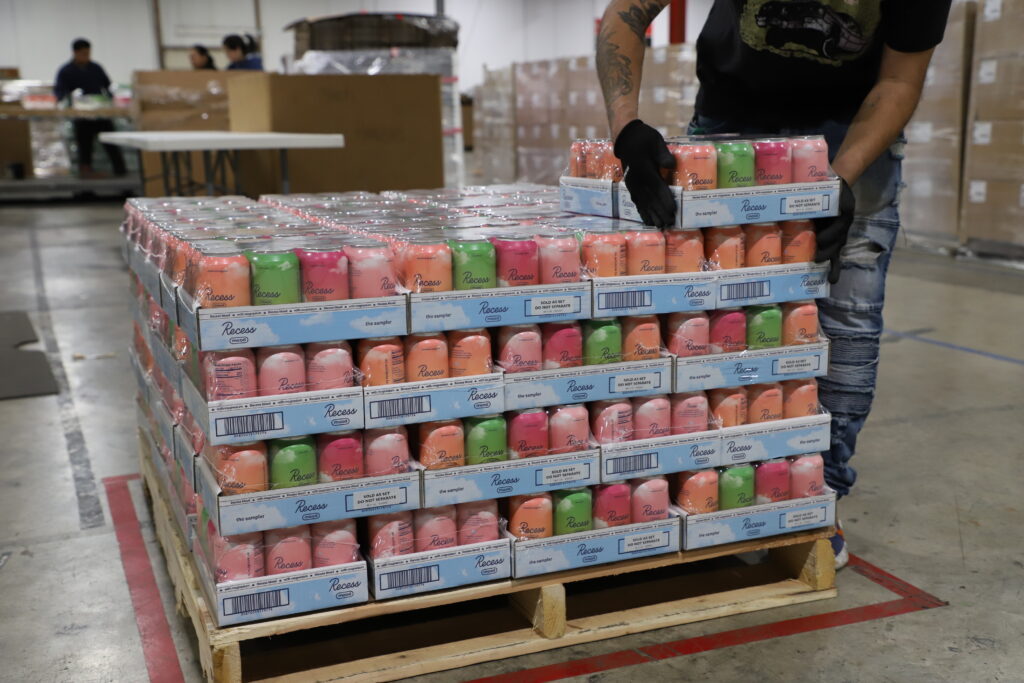
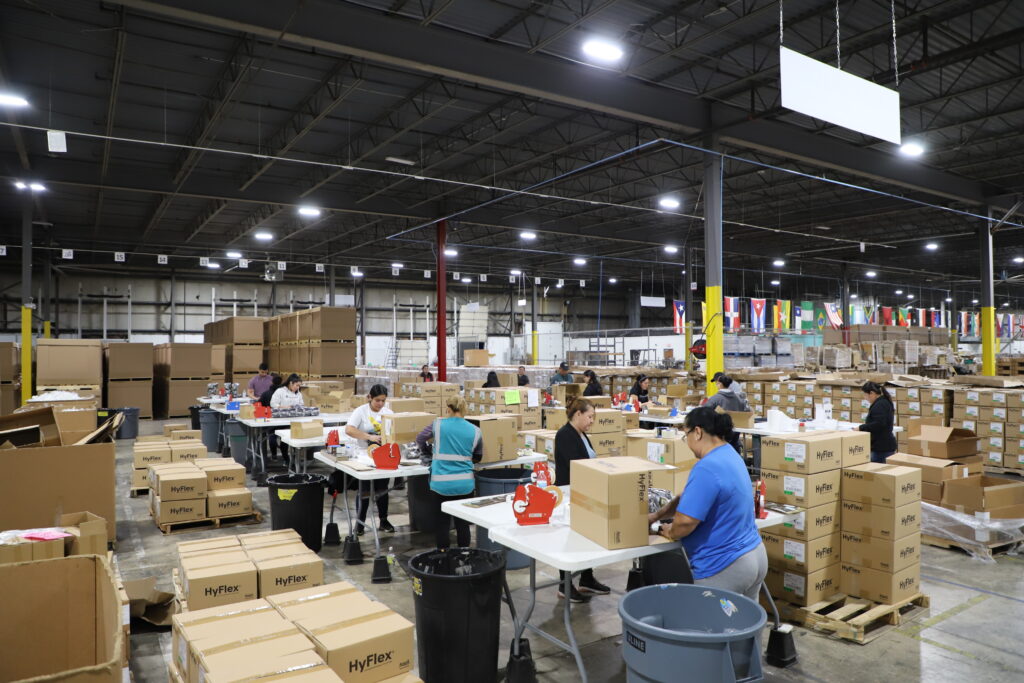
Fulfillment & Logistics Support
Improve efficiency and maintain client satisfaction by outsourcing key fulfillment operations. Our team leads will manage processes from pick and pack all the way to returns.
OUR CAPABILITIES
- Kitting & Assembly
- Labeling & Stickering
- Quality Inspection
- Sortation
- Repack & Rework
- Display Builds
- Incentives & Loyalty Marketing
- Returns
- Shrink Wrap & Secondary Packaging
- Refurbishing
- Packaging Solutions
-
Packaging Solutions
Stay on top of product alterations and capitalize on packaging as a marketing tool to your clients. Our team can focus on product appearance while ensuring safe and secure delivery to its destination.
OUR CAPABILITIES
- 3PL Fulfillment
- FBA Prep
- Kitting and Assembly
- Repack and Rework
- Display Builds
- Co-packing
- Labeling and Stickering
- Sortation
- Shrink Wrapping
- Primary and Secondary Packaging
- Assembly & Co-Manufacturing Solutions
-
Assembly & Co-Manufacturing Solutions
Reduce overhead costs and boost speed to market by shifting your assembly and co-manufacturing tasks to the Acción team. Our skilled team prioritizes quality and safety at every step.
OUR CAPABILITIES
- Kitting & Assembly
- Labeling & Stickering
- Quality Inspection
- Sortation
- Repack & Rework
- Display Builds
- Shrink Wrap & Secondary Packaging
- Incentives & Loyalty Marketing
- Returns Refurbishing
- Fulfillment by Amazon (FBA) Prep
-
Fulfillment by Amazon (FBA) Prep
Ensure your products are properly packaged and sent on time for Fulfillment by Amazon. Acción Performance prepares your items to fit necessary requirements, saving your team extra time and valuable resources.
OUR CAPABILITIES
- Kitting & Assembly
- Labeling & Stickering
- Quality Inspection
- Sortation
- Shrink Wrap & Secondary Packaging
- Repack & Rework
- Fulfillment & Logistics Support
-
Fulfillment & Logistics Support
Improve efficiency and maintain client satisfaction by outsourcing key fulfillment operations. Our team leads will manage processes from pick and pack all the way to returns.
OUR CAPABILITIES
- Kitting & Assembly
- Labeling & Stickering
- Quality Inspection
- Sortation
- Repack & Rework
- Display Builds
- Incentives & Loyalty Marketing
- Returns
- Shrink Wrap & Secondary Packaging
- Refurbishing
Location Matters
Our Indiana location brings your business the ultimate advantage. Ranked first in pass-through highways, the shortest distance to the median center of the U.S. population and more, Indiana provides opportunities for efficient and effective global logistics operations.
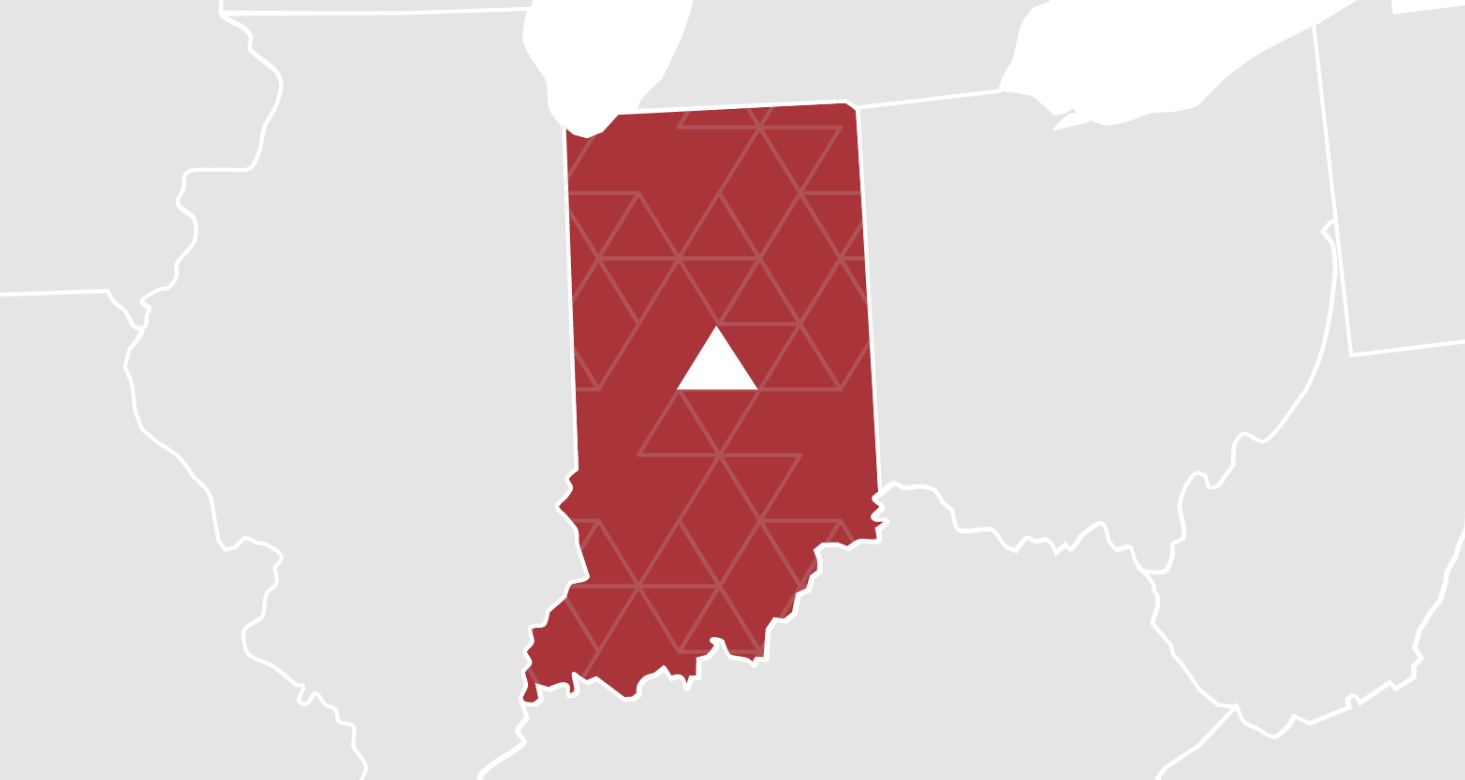
Solutions With Proven Results
On average, our clients’ labor costs are reduced by 15%
Team lead solutions constructed for cost-effectiveness
Strategic partnerships built for productivity & efficiency
Quick turnarounds to complete time-sensitive projects
Custom Solutions
See how the Acción team creates individualized solutions for our clients across industries to optimize their unique demands.